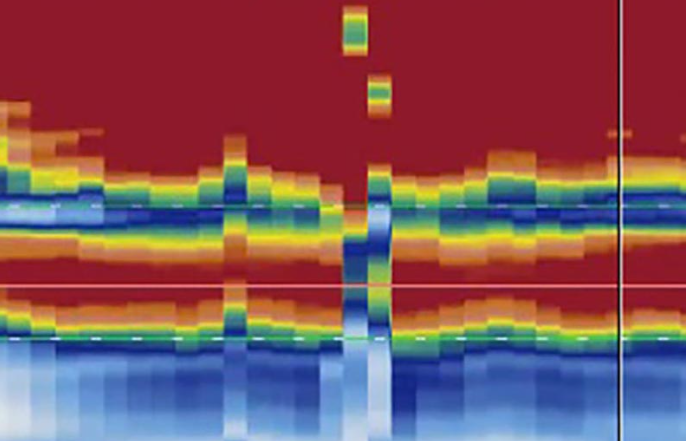
The Advantages of Phased Array Technology when Evaluating Welded Tubes Authored by Michael Moist, PAUT Global Sales Manager
Ultrasonic technology has been used for testing ERW welded pipe at various points in the manufacturing process for many years. ERW pipes are manufactured by cold forming a strip of steel into a cylindrical shape using forming rolls, and then having a high frequency electrical current pass between the strip edges increasing the temperature of the steel to its melting point.
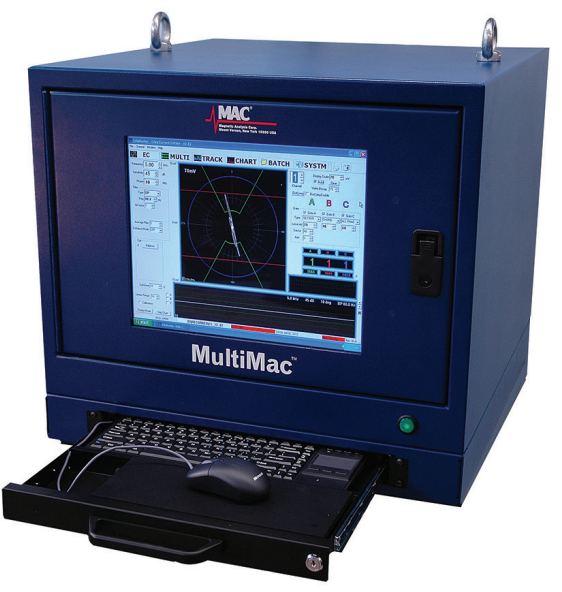
Quality Control for Copper Alloys
Magnetic Analysis Corp. offers a range of eddy current test instruments and systems for detecting surface and sub-surface defects in copper and copper alloy wire and bar. This versatile and generally cost-effective technology is being used in a broad range of wire and rod applications.

Testing Small Diameter Copper Rod & Wire During Drawing
A turn-key eddy current test system has been installed at a large copper rod and wire producer in China. The system is fully integrated with the company’s production line, and the quality of each coil of wire is accurately graded, allowing the manufacturer to match the coil quality with a specific customer’s needs and applications.
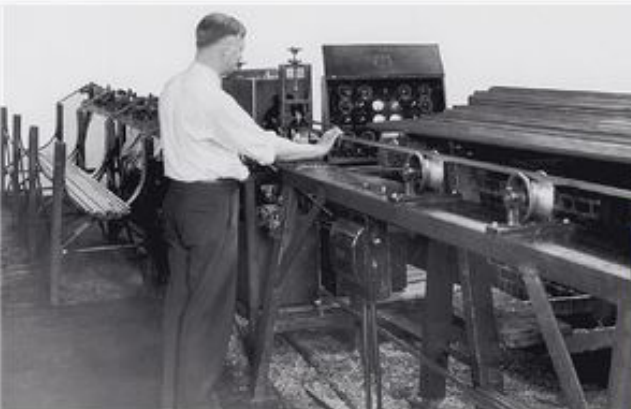
Testing Wire and Rod Over the Years
Magnetic Analysis Corp., (MAC) joins in congratulating WIRE on its 70 years covering the growth of the wire industry. A designer and manufacturer of nondestructive test systems, MAC was founded in 1928 and since then has made important contributions to testing technology for wire, cable and bar.
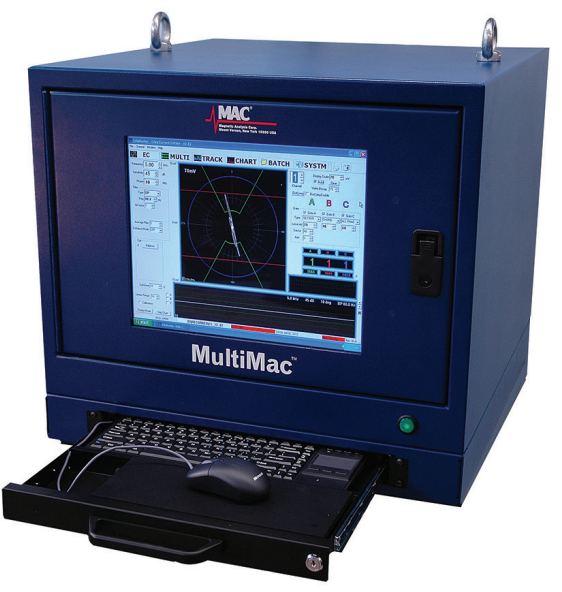
Supplying Testing Systems to the Industry Since 1928
Magnetic Analysis Corp (MAC), founded in 1928, offers a full range of eddy current test instruments and systems for detecting surface and sub-surface defects, including laps, slivers, and cracks in non-ferrous and ferrous wire and bar.
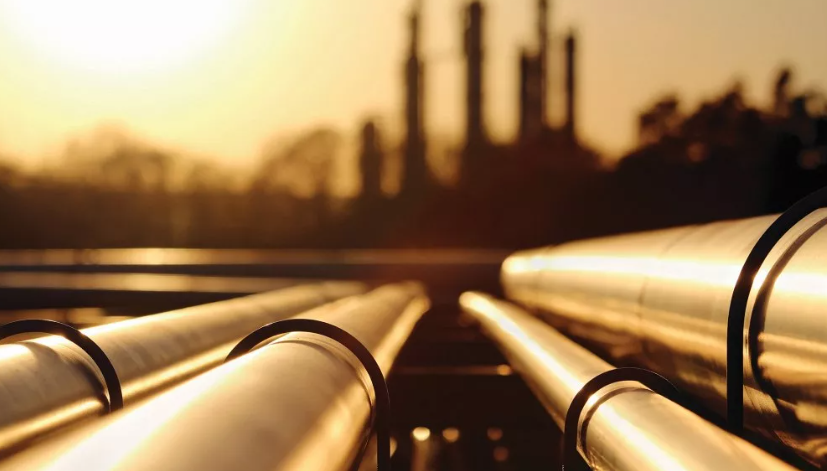
Choosing an NDT Process for Tube, Pipe Production Authored by Phil Meinczinger
As market pressures compel tube and pipe manufacturers to search for ways to increase productivity while maintaining adherence to strict quality standards, choosing the optimal inspection method and support system are more critical than ever.
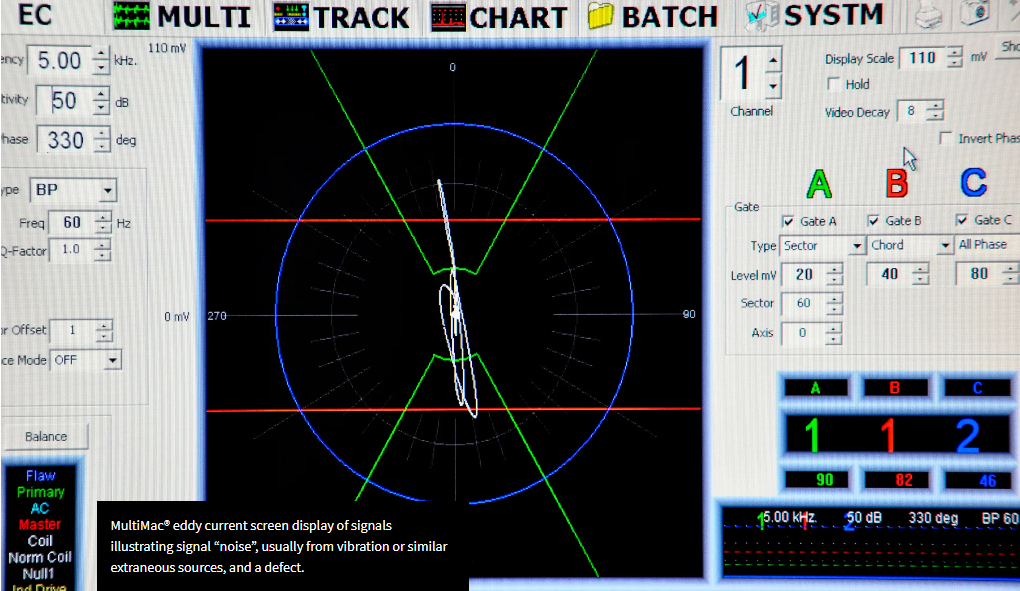
What Can Eddy Current Testing Do for Me Authored by Dean Isbell, ASNT Level III ET & UT
Since the development of eddy current testing in the early to mid-1900s this method has been used to detect defects and properties of many types of metals. The most common applications are testing tubular products for transverse defects, testing bar or wire products for longitudinal surface defects, and testing parts for defects and properties such as hardness.
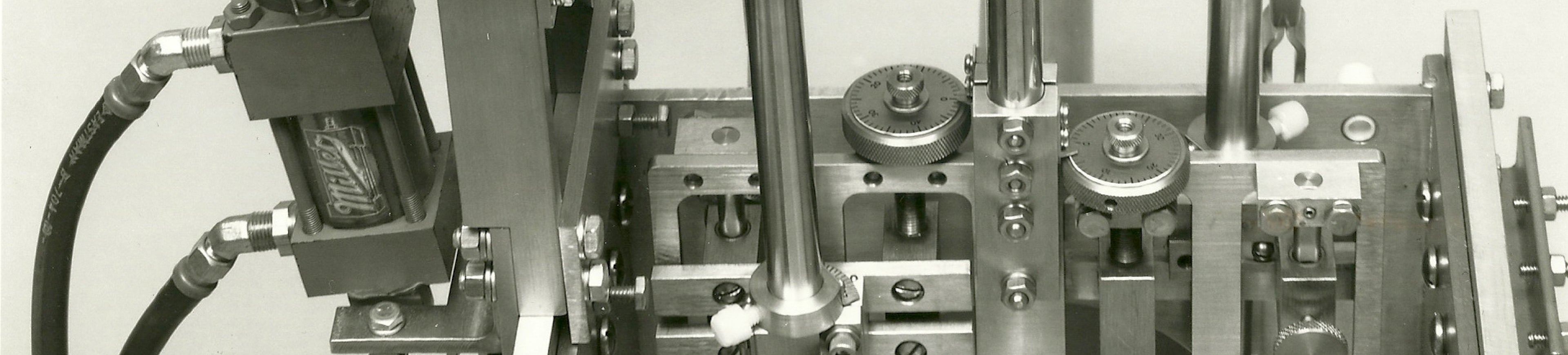
Magnetic Analysis Corp. Acquires TacTic™ Ultrasonic NDT Systems
Magnetic Analysis Corporation (MAC®), a designer and producer of nondestructive test instruments and systems since 1928, is pleased to announce the asset acquisition of TacTic™, a Division of Laboratory Testing Inc. (LTI), effective February 28, 2022. Originally founded as TAC Technical Instrument Corp.
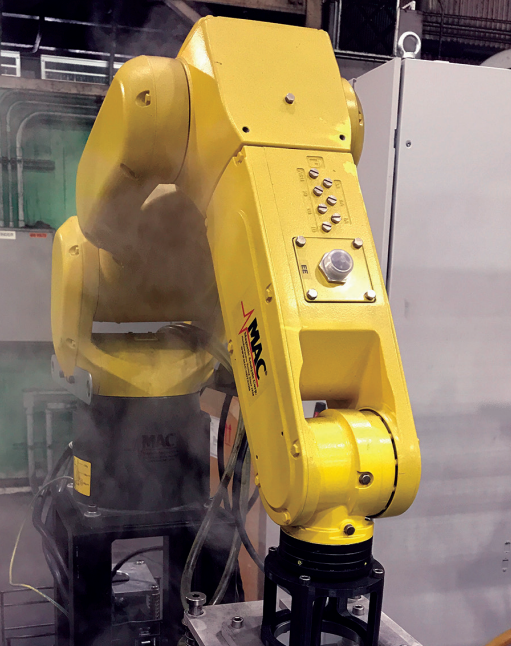
Magnetic Analysis Corp. to Feature NDT Instruments at Tube 2022 in Germany
MAGNETIC Analysis Corp will feature non-destructive testing instruments and systems for testing tube, pipe, and bar at stand number 6H20 at Tube 2022 Düsseldorf in Germany in June. Highlights at the booth will include MAC’s latest Echomac® Systems for testing ERW welded tube.
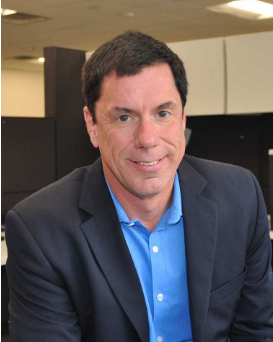
Interview with MAC’s Vice President of Sales, Michael Moist
Magnetic Analysis Corp. (MAC) is a company established over 90 years ago providing non-destructive testing (NDT) equipment for the metals industry, primarily producers of tube, pipe, bar, wire, and parts. The company’s focus is in-line automated testing systems ensuring the identification of defects that would impair the functionality of the product.
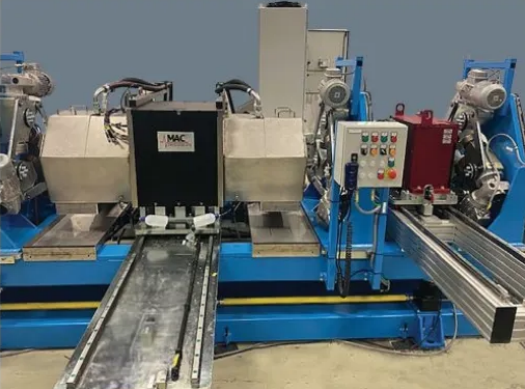
Automated Test System for Cold Finishing Specialty Steel Mill
Increasing demands for high-quality steel rod and bar requires effective nondestructive (NDT) testing to ensure producers can meet their customer’s needs. As specifications become ever more stringent, NDT technology is consistently evolving new capabilities, adapting to new conditions and improving integration with mill operations.
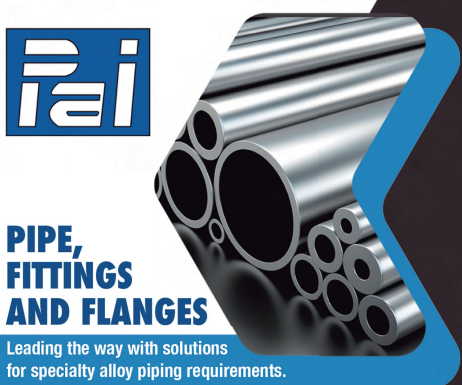
Using NDT to Ensure Product Quality Authored by Joseph Baldauff, ASNT Level III ET and UT
Industrial heat exchanger users, aerospace, medical, and some military applications require the highest quality materials and also demand high inspection levels for long intermediate products (wire, tube, and bars). Surprisingly, automotive materials can also require the highest quality because defects in safety-critical components or parts integral to engine lifetime or fuel systems can lead to huge expenses.