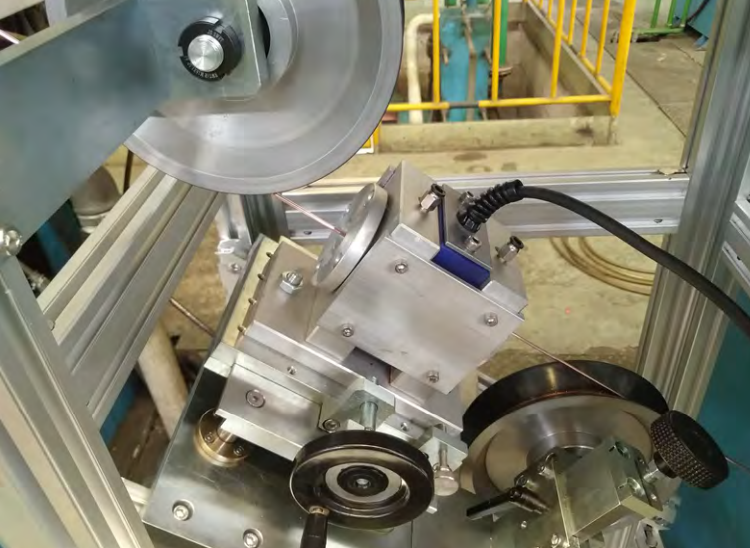
How to Use Eddy Current Technology to Test Ferrous and Non-Ferrous Wire” Authored by Troy Libby, Engineering Manager
Eddy Current inspection is a technique used for detecting surface seams, cracks, pits, slivers, and internal discontinuities in ferrous and non-ferrous wire. Different test sensor configurations, including encircling coil and rotary probes, can be used. When using encircling coil eddy current testing, the wire passes through the coil excited by an alternating current with one or more drive signals.
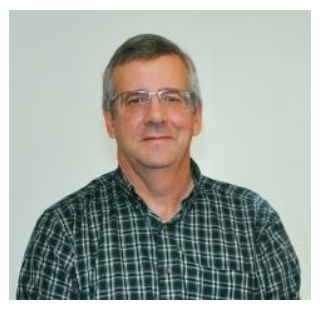
Magnetic Analysis Corp. Announces New CEO
Magnetic Analysis Corp., a global leader in instruments and systems for the nondestructive testing of metals, is pleased to announce the appointment of Daniel Lawrence as President and Chief Executive Officer effective November 6th, 2023.
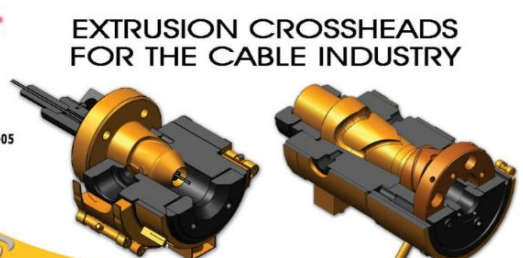
Latest Eddy Current Testing Model to be Showcased at Düsseldorf 2024
Magnetic Analysis Corp. will feature the Minimac® II at its booth. This latest addition to MAC’s range of eddy current test instruments for detecting surface and sub-surface defects such as laps, slivers and cracks in nonferrous and ferrous wire and rod, features an embedded processor host computer, and can be supplied with one or two test channels.
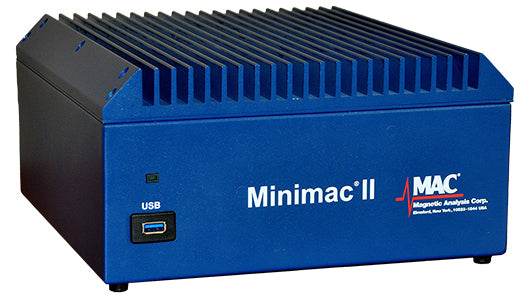
Test Systems for the Wire and Cable Industry
Magnetic Analysis Corp. will be featuring the “Minimac II” at its booth which is to find in the tube section. Wire producers are invited to come over to see products that are applicable to both wire and tube.
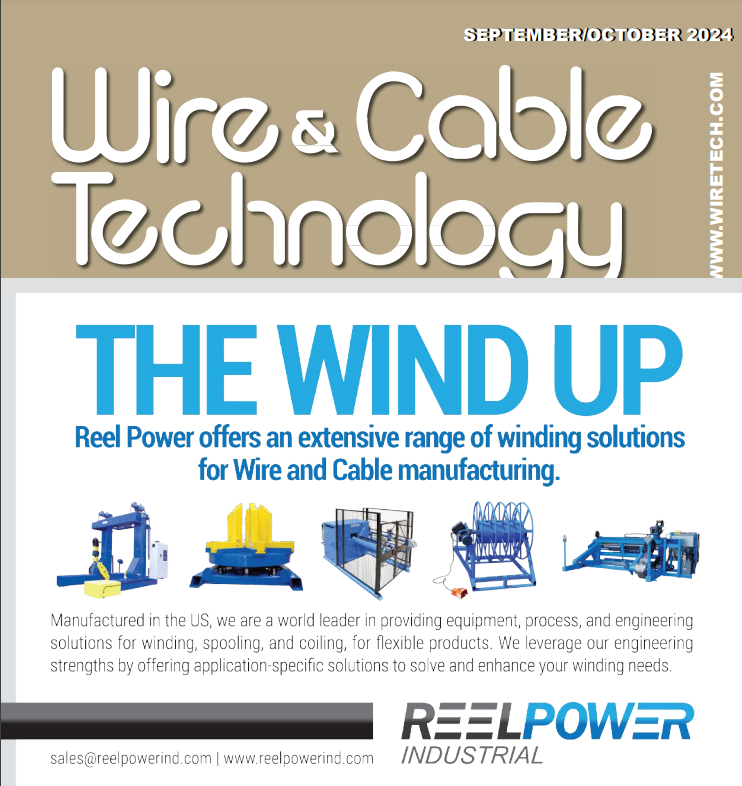
Vendors that Become Partners: Collaborate on Effective NDT to Ensure High-Quality Products
One small handful of rejected materials, identified during a run of 30,000 high-precision components, is one handful too many,” asserts John Pechan, Chief Operating Officer at Round Ground Metals® (RGM®).
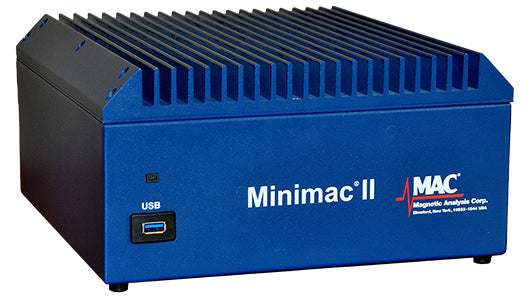
MAC to Exhibit at Wire Expo 2024
Minimac® II, Magnetic Analysis Corp.’s latest eddy current tester, will be featured at Booth #607 at Wire Expo. This addition to MAC’s range of eddy current test instruments for detecting surface and sub-surface defects such as laps, slivers and cracks in non ferrous and ferrous wire and rod, features an embedded processor host computer, and can be supplied with one or two test channels.
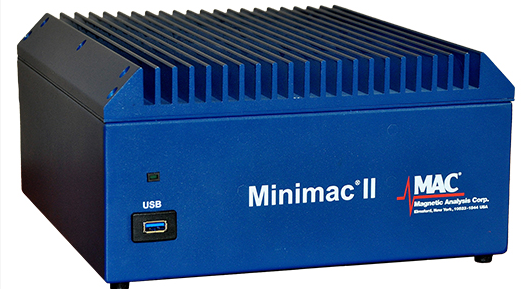
MAC® & Inmar to Feature NDT Test Systems for Tube, Bar and Wire at Tube India 2024
MAC is pleased to announce its participation in Tube India, one of the premier trade shows for the tube and pipe industry. NDT Test instruments and systems for inspecting tube, pipe, bar, and wire will be featured at our booth B 30 in Hall 2.
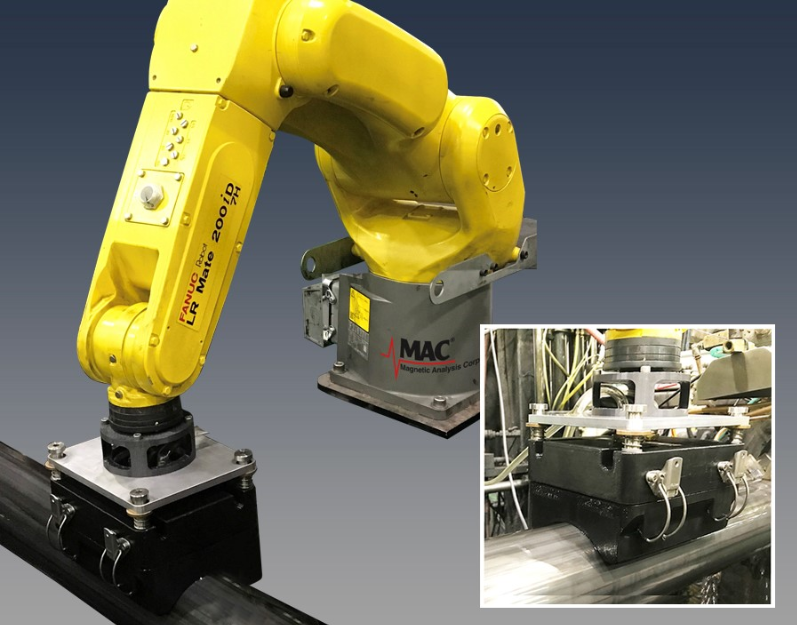
MAC® at the 2024 Pipe and Tube Conference in Omaha
Magnetic Analysis Corporation (MAC®) is excited to announce its participation in the 2024 Pipe and Tube Conference, taking place on November 13-14 at the Kimpton Cottonwood Hotel in Omaha, Nebraska. This year’s conference promises to be a dynamic gathering for industry professionals, featuring insightful sessions on cutting-edge technologies and networking opportunities.

AUTOMOTIVE TUBE
Precision tubes for the automotive industry must meet the highest performance requirements. MAC’s® Eddy Current, Flux Leakage and Ultrasonic systems are often used to inspect tubes destined to be cut into short lengths to be fabricated into a critical automotive component.
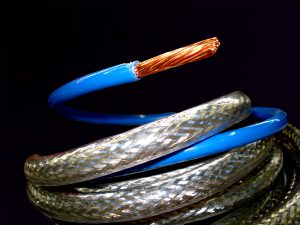
WIRE AND ROD
Eddy Current technology is the go-to wire and cable testing method for checking continuity, alloy, surface flaws and other conditions as well as for locating welds and splices. MAC® instruments can handle a range of metal wire including cut lengths, continuous production, stranded, multi-conductor and insulated cable.
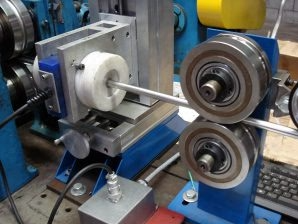
WELDED TUBE
There are many welding processes and many tubing configurations and sizes. MAC has extensive experience testing tubes and pipes using eddy current, ultrasonic, and flux leakage technologies. We have a large base of testing equipment lines being used to meet the many different ASTM, API, EN, ISO and other industry quality standards and or customer driven quality requirements.
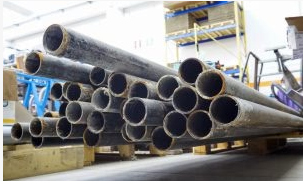
TUBE ENDS
All nondestructive test (NDT) methods have some limitation in regard to testing to the very end of a tube. These “untested ends” must be cut off, resulting in a substantial loss of product and revenue. To avoid this loss, a manufacturer needs to develop a method to test these ends to meet the tube integrity requirement.