At Magnetic Analysis Corporation, we understand the importance of precision and reliability in testing tube and pipe products. Our Spin-the-Tube systems, integrated with ultrasonic and/or magnetic flux leakage technologies, are one of our comprehensive solutions for detecting a wide range of defects and conditions in tube and pipe products.
Whether it's detecting longitudinal and transverse flaws, measuring, wall thickness, identifying lamination, or testing through-drilled holes, our systems deliver reliable performance for the integrity of your products.
Three Spin the Tube system options:
Using Echomac® FD6 Technology
For Flaw Detection, Thickness & Dimensional Measurement in Tube & Bar
- Versatile Ultrasonic tester with superior performance and versatile, intuitive operation.
- For full inspection of tubes, pipes and bars, plate and weld.
- Operate on or off line
- Upgrade and/or replace older ultrasonic testers
- Use with rotary, spin-the-tube, squirter and bubbler installations.
You may also like
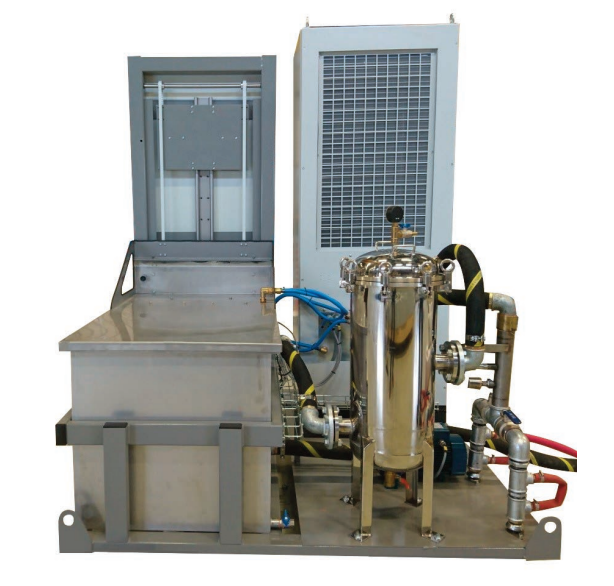
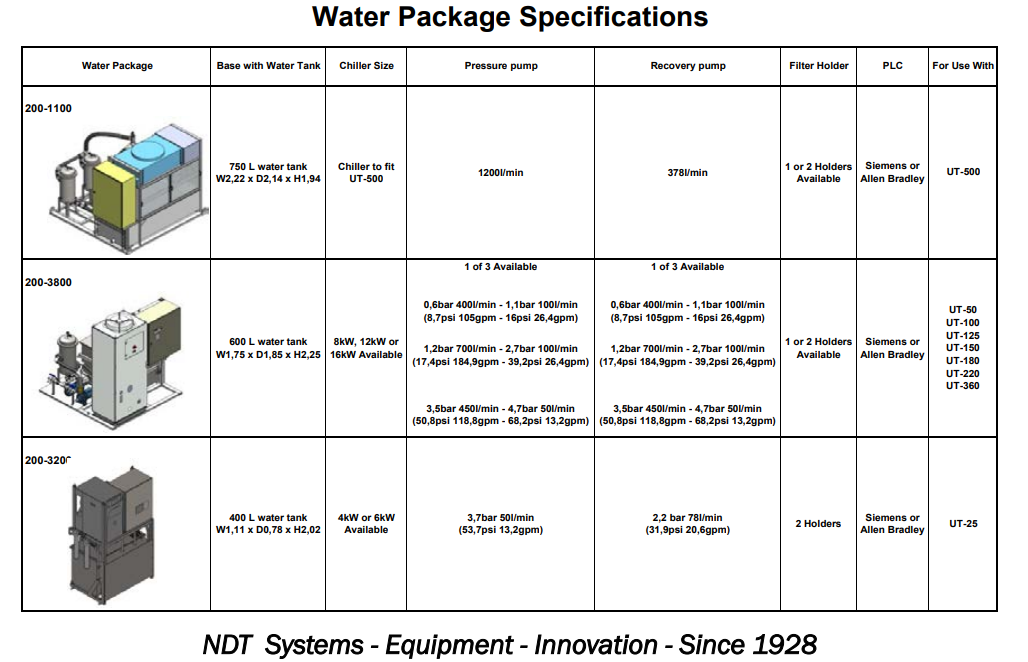
WATER PACKAGE
For use with Magnetic Analysis Test Systems
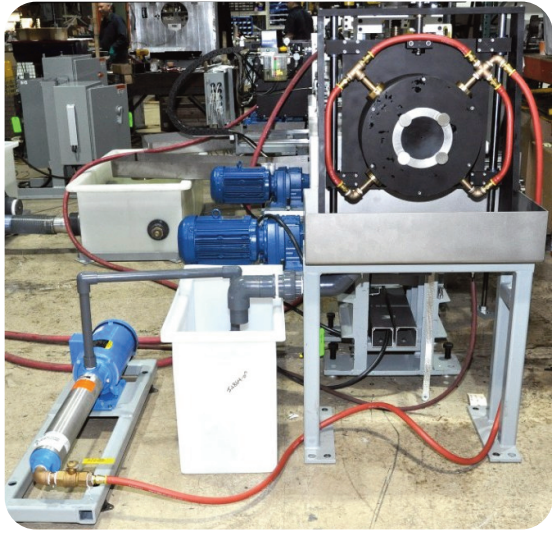
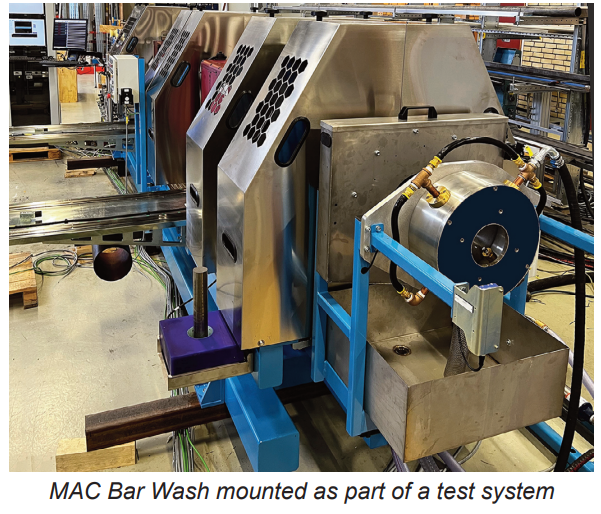
MAC BAR WASH
Prevent False Test Signals from Contaminated Bar & Tube Surfaces & Reduce Rotary Cleaning Downtime.
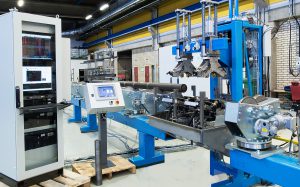
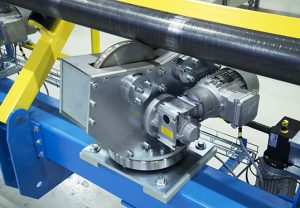
ECHOMAC® FULL BODY TESTER
Ultrasonic Spin-the-Tube Inspection System with APC Pitch Control Technology
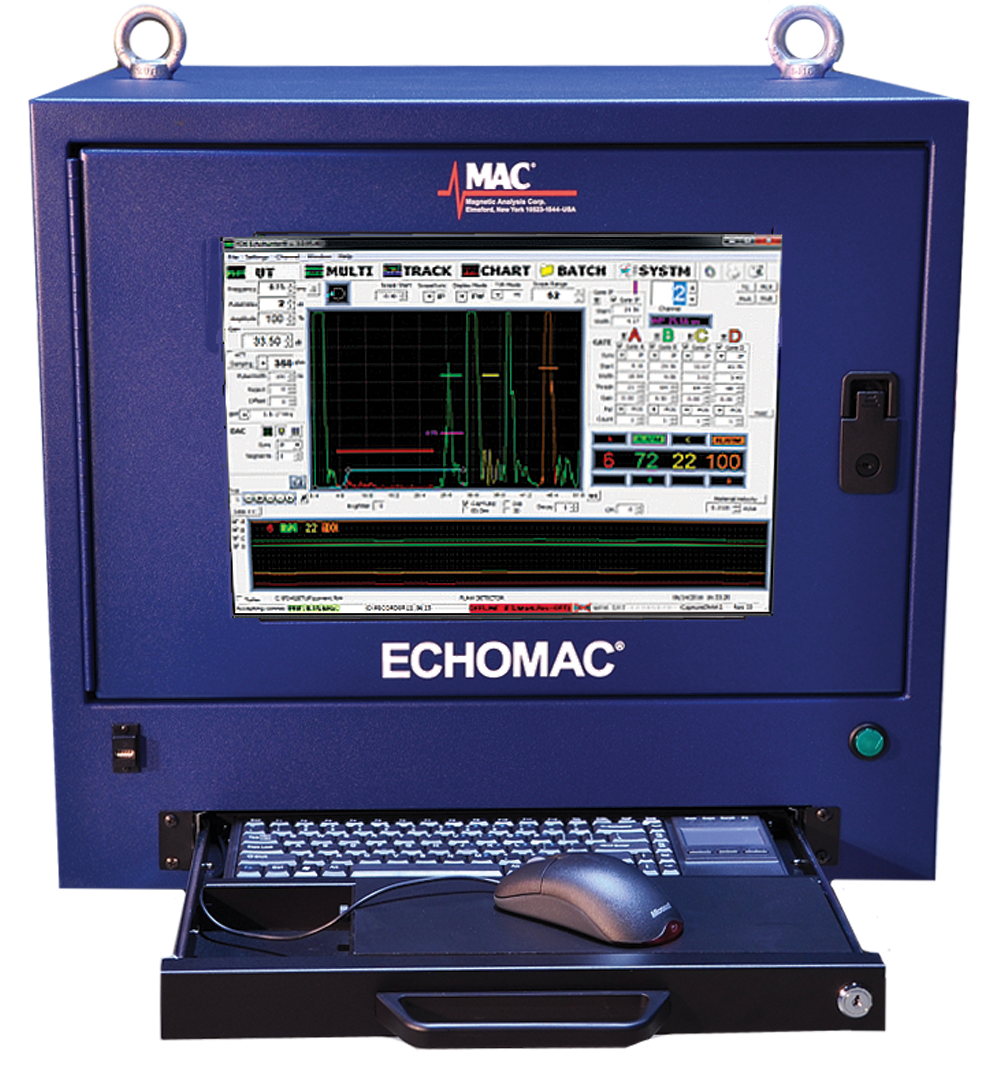
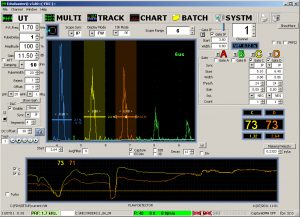
ECHOMAC® FD6 MULTICHANNEL UT
Ultrasonic Instrument for Flaw Detection, Thickness, and Dimensional Measurement in Tube & Bar